The chip industry is out of power
In recent years, the artificial intelligence industry has developed rapidly, and chips, as its core components, have always been a focus of attention. However, at the Bosch Connected World Conference 2024, Tesla CEO Elon Musk proposed a viewpoint: by 2025, what may trouble the AI industry may no longer be the shortage of chips, but the tight supply of electricity. At the same time, multiple media reports have indicated that TSMC, a major chip foundry, is also facing electricity cost challenges. According to reports, Taiwan is considering increasing TSMC's electricity prices by up to 30%.
Chip manufacturing is a highly complex and energy-intensive process. From the melting of silicon, to the use of high-power lasers for lithography, to the creation and maintenance of a vacuum state, as well as continuous cleaning work, every step requires a significant amount of electrical support. Statistics show that semiconductor manufacturing plants consume up to 100 megawatt-hours of electricity per hour, equivalent to the electricity usage of more than 80,000 North American households. This means that as the demand for chips in the artificial intelligence industry continues to grow, the pressure on electricity supply will also increase.
Advertisement
With the rapid development and application of artificial intelligence, there has been much discussion about its energy consumption. How energy-intensive is artificial intelligence? The energy consumed to generate nine photos can charge a smartphone.
A team composed of artificial intelligence developers Hugging Face and researchers from Carnegie Mellon University, using a self-developed tool called Code Carbon, compared the energy consumption and carbon emission data of the 16 most popular open-source models on the HuggingFace Hub. The data shows that the electricity consumed by generative AI to generate 1,000 images is between 0.06 and 2.9 kilowatt-hours (kWh), with the median close to 1.35 kWh. In comparison, the energy required to charge a typical smartphone is only 0.012 kWh. This means that the energy consumed to generate about nine (median) artificial intelligence images is equivalent to the energy needed to charge a fully powered smartphone. If users employ the least efficient image generation model, then the energy consumed to generate one image is enough to charge a typical smartphone once, and in the worst case, it could even charge it twice.
The high energy consumption implies an increase in carbon emissions.
As the scale of models expands and the quality of generated images improves, the required energy consumption and carbon emissions will also increase further. The energy consumption is related to the issue of carbon emissions, with the carbon dioxide emissions produced during the generation of each image ranging from 0.1 to 0.5 grams, with outliers potentially reaching 2 grams of carbon dioxide. This means that the emissions produced by generating 1,000 images are equivalent to the emissions produced by a typical car traveling 6.5 kilometers.
The energy consumption and carbon emission issues in the field of artificial intelligence image generation cannot be ignored.
01
TSMC consumes 7% of the island's electricity
Let's take a closer look at the electricity consumption issues in the chip industry.In 2020, TSMC's EUV photolithography machines consumed as much as 10 billion kWh of electricity, accounting for over 50% of TSMC's total electricity usage. As TSMC continuously expands its advanced processes, it must keep adding photolithography machines, leading to a year-on-year increase in electricity demand.
TSMC's electricity consumption in 2020 was 16 billion kWh, representing about 5.9% of Taiwan Power Company's (Taipower) sales volume; in 2021, it rapidly grew to 19.19 billion kWh, accounting for 7.2% of Taipower's sales volume, with an electricity growth rate as high as 20%, surpassing the electricity consumption of Taipei City, which has a population of over 2.7 million. According to Deloitte's estimates, by 2025, TSMC alone will account for 12.5% of the overall energy consumption in Taiwan, China.
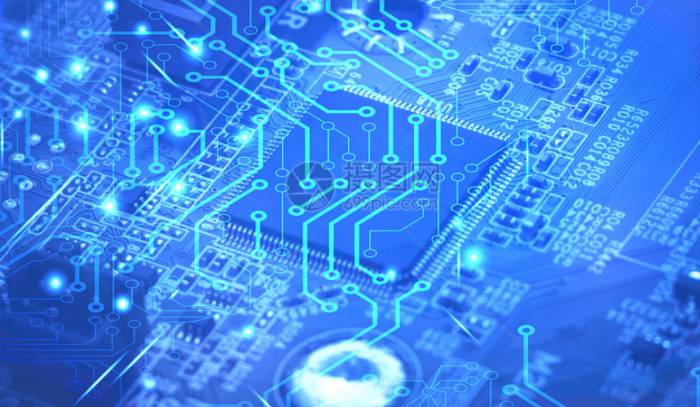
Furthermore, wafer manufacturing requires an ultra-clean production environment, and the entire cleanroom needs to be cooled and temperature-controlled to maintain a steady state around 22°C, consuming a significant amount of electrical energy daily for normal operation; to heat-treat equipment and ion equipment for handling the high temperatures generated during the chip production process, the power consumption involved in this part is also extremely astonishing. Deloitte estimates that by 2028, TSMC's electricity consumption in Taiwan, China, could reach an astonishing 15%.
With the advancement of global climate change and energy transition, the stability of electricity supply has become a global issue. Faced with such enormous electricity consumption, the biggest problem for the chip industry is that unstable power supply will directly affect factory output. Especially in developing countries, the issues of insufficient and unstable power supply are particularly prominent. Previously, Intel's reason for shelving its investment plan in Vietnam was "concerns about the stability of Vietnam's power supply."
In this context, if the artificial intelligence industry continues to develop at the current rate of energy consumption, the tightness of electricity supply is likely to become a bottleneck restricting its development. Moreover, tight electricity supply may also pose challenges to the sustainable development of the artificial intelligence industry. As people pay more and more attention to environmental protection and sustainable development, an increasing number of companies and countries are beginning to focus on green energy as a priority for development. However, if the energy consumption of the artificial intelligence industry continues to grow, its demand for green energy will also increase continuously. This may make the supply of green energy more tense, thereby affecting the sustainable development of the entire industry.
02
No electricity, no chips
Looking back at TSMC's electricity consumption, the consumption of TSMC's factories in Taiwan, China, is already so large, and it is conceivable that the scale of electricity consumption of global wafer fabs is even larger. There are many reasons for the high electricity consumption of wafer fabs, and of course, the most direct point is that without electricity, chips cannot be made.
Looking more specifically, the chip industry's requirements for electricity are somewhat demanding.
In terms of electricity usage characteristics, TSMC requires 24-hour continuous processes, which are full-time electricity usage, with an annual load rate of 80% to 90%. Among them, in the advanced process capacity part, it is highly likely to be in a full load state, and the daily electricity consumption curve distribution of the production factory should maintain a peak in electricity usage throughout the day. At the same time, with the update of processes and the expansion of production, TSMC's electricity consumption will also increase.To ensure a stable power supply for TSMC, Taipower has implemented supporting power supply measures in Hsinchu Science Park, Central Taiwan Science Park, and Southern Taiwan Science Park. Hsinchu Science Park is supported by a round-the-clock power plant and offshore photovoltaic power; Central Taiwan Science Park is backed by Taichung Power Plant and offshore wind power, while the south lacks offshore wind power, and Southern Taiwan Science Park primarily relies on Taipower's Xingda Power Plant for its main power source. The concept is that Taipower's power plants directly supply the science parks related to TSMC. To ensure TSMC's production, relevant departments have provided a double insurance by using dual circuits to prevent power outages and ensure uninterrupted production processes for TSMC. Even in the event of an accident, TSMC itself also has backup power generation equipment.
Such high electricity consumption, for chip companies, means that the demand for low-carbon behind it is growing. The chip industry has also tried various explorations to become greener. Measures that the chip industry can take include improving the energy efficiency and speed of other processes in addition to the current chip manufacturing process: for example, LEED certified buildings, a technology that the industry has been using for ten years to enhance sustainable development capabilities. The US LEED system is an international green building certification system.
Of course, the most important thing is still the application of green electricity. According to Deloitte data, renewable energy can reduce the industry's wafer fabs' energy consumption intensity (watt-hours per dollar) from nearly 240 in 2020 to 219 in 2022, and it is expected to drop to 206 by 2024. In addition, the proportion of renewable energy usage is expected to rise at a faster rate than the decline in energy consumption intensity: it is projected that by 2024, renewable energy will account for 28% of the energy mix, double that of 2020.
In the final analysis, power issues and energy issues are all environmental protection topics. More and more companies are putting their environmental protection "KPIs" on the table. Intel announced in April 2022 its commitment to achieving net-zero greenhouse gas emissions. By 2030, it aims to reduce greenhouse gas emissions from the supply chain by 30% compared to what they would be without investment and action; while also improving energy efficiency and reducing the carbon footprint of our products and platforms. TSMC stated in its CSR (sustainability) report that by 2030, 100% green electricity will be used for non-production electricity, but only 25% green electricity can be used for production electricity.
03
Environmental protection is not just about saving on electricity costs.
With the continuous advancement of technology and the expansion of the global electronics market, the semiconductor industry is developing at an unprecedented speed. For semiconductor companies, improving sustainability is not only a social responsibility but also a business return. In future development, semiconductor companies need to continuously strengthen their investment and innovation in environmental protection and sustainable development to adapt to increasingly severe environmental challenges and market demands. In today's era that increasingly focuses on environmental protection and sustainable development, semiconductor companies are facing unprecedented challenges and opportunities. As the global awareness of green energy and environmental protection continues to grow, the proportion and composition of green electricity in the production process of semiconductor companies have attracted more and more attention. For semiconductor companies, environmental awareness is not only a social responsibility but also a business return. Improving sustainability not only helps the long-term development of the company but also brings many practical benefits.
To achieve this goal, semiconductor companies can take a series of measures. First, strengthen technological research and development and innovation, and promote the research and application of green production technology. By developing more environmentally friendly and efficient production technologies, energy consumption and environmental pollution can be further reduced. Second, establish a sound green supply chain management system to ensure that every link in the supply chain meets the requirements of environmental protection and sustainable development. In addition, strengthening employee training and awareness enhancement, and cultivating a team with environmental awareness and sustainable development concepts, is also crucial.
By reducing energy consumption and waste emissions, companies can significantly reduce production costs. Secondly, as society's awareness of environmental protection increases, improving sustainability helps semiconductor companies attract and retain talent, and also wins more consumer trust and support. In addition, improving sustainability also helps reduce the vulnerability of the semiconductor supply chain, ensuring the stability and security of the supply chain.In the talent competition of the semiconductor industry, environmental protection also occupies an important position. The semiconductor industry is facing a competition for technical talent with several other industries, so maintaining a good environmental record is particularly important. Especially in attracting young employees, companies with a good record of sustainable development are more attractive. According to Deloitte's 2023 survey of Generation Z and Millennials, one-sixth of the respondents have already changed jobs or industries due to climate issues, and another quarter of the respondents plan to do so in the future. This trend indicates that the importance of environmental protection and sustainable development in the recruitment of talent in the semiconductor industry cannot be ignored.
In recent years, the artificial intelligence industry has developed rapidly, and chips, as its core components, have always been a focus of attention. However, at the Bosch Connected World Conference 2024, Tesla CEO Elon Musk proposed a viewpoint: by 2025, what may trouble the AI industry may no longer be the shortage of chips, but the tight supply of electricity. At the same time, multiple media reports have indicated that TSMC, a major chip foundry, is also facing electricity cost challenges. According to reports, Taiwan is considering increasing TSMC's electricity prices by up to 30%.
Chip manufacturing is a highly complex and energy-intensive process. From the melting of silicon, to the use of high-power lasers for lithography, to the creation and maintenance of a vacuum state, as well as continuous cleaning work, every step requires a significant amount of electrical support. Statistics show that semiconductor manufacturing plants consume up to 100 megawatt-hours of electricity per hour, equivalent to the electricity usage of more than 80,000 North American households. This means that as the demand for chips in the artificial intelligence industry continues to grow, the pressure on electricity supply will also increase.
Advertisement
With the rapid development and application of artificial intelligence, there has been much discussion about its energy consumption. How energy-intensive is artificial intelligence? The energy consumed to generate nine photos can charge a smartphone.
A team composed of artificial intelligence developers Hugging Face and researchers from Carnegie Mellon University, using a self-developed tool called Code Carbon, compared the energy consumption and carbon emission data of the 16 most popular open-source models on the HuggingFace Hub. The data shows that the electricity consumed by generative AI to generate 1,000 images is between 0.06 and 2.9 kilowatt-hours (kWh), with the median close to 1.35 kWh. In comparison, the energy required to charge a typical smartphone is only 0.012 kWh. This means that the energy consumed to generate about nine (median) artificial intelligence images is equivalent to the energy needed to charge a fully powered smartphone. If users employ the least efficient image generation model, then the energy consumed to generate one image is enough to charge a typical smartphone once, and in the worst case, it could even charge it twice.
The high energy consumption implies an increase in carbon emissions.
As the scale of models expands and the quality of generated images improves, the required energy consumption and carbon emissions will also increase further. The energy consumption is related to the issue of carbon emissions, with the carbon dioxide emissions produced during the generation of each image ranging from 0.1 to 0.5 grams, with outliers potentially reaching 2 grams of carbon dioxide. This means that the emissions produced by generating 1,000 images are equivalent to the emissions produced by a typical car traveling 6.5 kilometers.
The energy consumption and carbon emission issues in the field of artificial intelligence image generation cannot be ignored.
01
TSMC consumes 7% of the island's electricity
Let's take a closer look at the electricity consumption issues in the chip industry.In 2020, TSMC's EUV photolithography machines consumed as much as 10 billion kWh of electricity, accounting for over 50% of TSMC's total electricity usage. As TSMC continuously expands its advanced processes, it must keep adding photolithography machines, leading to a year-on-year increase in electricity demand.
TSMC's electricity consumption in 2020 was 16 billion kWh, representing about 5.9% of Taiwan Power Company's (Taipower) sales volume; in 2021, it rapidly grew to 19.19 billion kWh, accounting for 7.2% of Taipower's sales volume, with an electricity growth rate as high as 20%, surpassing the electricity consumption of Taipei City, which has a population of over 2.7 million. According to Deloitte's estimates, by 2025, TSMC alone will account for 12.5% of the overall energy consumption in Taiwan, China.
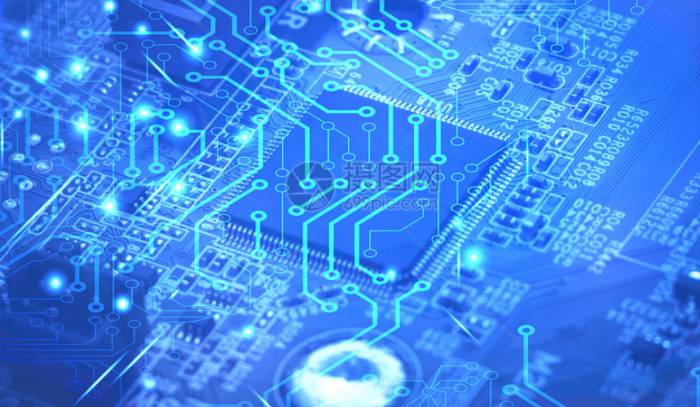
Furthermore, wafer manufacturing requires an ultra-clean production environment, and the entire cleanroom needs to be cooled and temperature-controlled to maintain a steady state around 22°C, consuming a significant amount of electrical energy daily for normal operation; to heat-treat equipment and ion equipment for handling the high temperatures generated during the chip production process, the power consumption involved in this part is also extremely astonishing. Deloitte estimates that by 2028, TSMC's electricity consumption in Taiwan, China, could reach an astonishing 15%.
With the advancement of global climate change and energy transition, the stability of electricity supply has become a global issue. Faced with such enormous electricity consumption, the biggest problem for the chip industry is that unstable power supply will directly affect factory output. Especially in developing countries, the issues of insufficient and unstable power supply are particularly prominent. Previously, Intel's reason for shelving its investment plan in Vietnam was "concerns about the stability of Vietnam's power supply."
In this context, if the artificial intelligence industry continues to develop at the current rate of energy consumption, the tightness of electricity supply is likely to become a bottleneck restricting its development. Moreover, tight electricity supply may also pose challenges to the sustainable development of the artificial intelligence industry. As people pay more and more attention to environmental protection and sustainable development, an increasing number of companies and countries are beginning to focus on green energy as a priority for development. However, if the energy consumption of the artificial intelligence industry continues to grow, its demand for green energy will also increase continuously. This may make the supply of green energy more tense, thereby affecting the sustainable development of the entire industry.
02
No electricity, no chips
Looking back at TSMC's electricity consumption, the consumption of TSMC's factories in Taiwan, China, is already so large, and it is conceivable that the scale of electricity consumption of global wafer fabs is even larger. There are many reasons for the high electricity consumption of wafer fabs, and of course, the most direct point is that without electricity, chips cannot be made.
Looking more specifically, the chip industry's requirements for electricity are somewhat demanding.
In terms of electricity usage characteristics, TSMC requires 24-hour continuous processes, which are full-time electricity usage, with an annual load rate of 80% to 90%. Among them, in the advanced process capacity part, it is highly likely to be in a full load state, and the daily electricity consumption curve distribution of the production factory should maintain a peak in electricity usage throughout the day. At the same time, with the update of processes and the expansion of production, TSMC's electricity consumption will also increase.To ensure a stable power supply for TSMC, Taipower has implemented supporting power supply measures in Hsinchu Science Park, Central Taiwan Science Park, and Southern Taiwan Science Park. Hsinchu Science Park is supported by a round-the-clock power plant and offshore photovoltaic power; Central Taiwan Science Park is backed by Taichung Power Plant and offshore wind power, while the south lacks offshore wind power, and Southern Taiwan Science Park primarily relies on Taipower's Xingda Power Plant for its main power source. The concept is that Taipower's power plants directly supply the science parks related to TSMC. To ensure TSMC's production, relevant departments have provided a double insurance by using dual circuits to prevent power outages and ensure uninterrupted production processes for TSMC. Even in the event of an accident, TSMC itself also has backup power generation equipment.
Such high electricity consumption, for chip companies, means that the demand for low-carbon behind it is growing. The chip industry has also tried various explorations to become greener. Measures that the chip industry can take include improving the energy efficiency and speed of other processes in addition to the current chip manufacturing process: for example, LEED certified buildings, a technology that the industry has been using for ten years to enhance sustainable development capabilities. The US LEED system is an international green building certification system.
Of course, the most important thing is still the application of green electricity. According to Deloitte data, renewable energy can reduce the industry's wafer fabs' energy consumption intensity (watt-hours per dollar) from nearly 240 in 2020 to 219 in 2022, and it is expected to drop to 206 by 2024. In addition, the proportion of renewable energy usage is expected to rise at a faster rate than the decline in energy consumption intensity: it is projected that by 2024, renewable energy will account for 28% of the energy mix, double that of 2020.
In the final analysis, power issues and energy issues are all environmental protection topics. More and more companies are putting their environmental protection "KPIs" on the table. Intel announced in April 2022 its commitment to achieving net-zero greenhouse gas emissions. By 2030, it aims to reduce greenhouse gas emissions from the supply chain by 30% compared to what they would be without investment and action; while also improving energy efficiency and reducing the carbon footprint of our products and platforms. TSMC stated in its CSR (sustainability) report that by 2030, 100% green electricity will be used for non-production electricity, but only 25% green electricity can be used for production electricity.
03
Environmental protection is not just about saving on electricity costs.
With the continuous advancement of technology and the expansion of the global electronics market, the semiconductor industry is developing at an unprecedented speed. For semiconductor companies, improving sustainability is not only a social responsibility but also a business return. In future development, semiconductor companies need to continuously strengthen their investment and innovation in environmental protection and sustainable development to adapt to increasingly severe environmental challenges and market demands. In today's era that increasingly focuses on environmental protection and sustainable development, semiconductor companies are facing unprecedented challenges and opportunities. As the global awareness of green energy and environmental protection continues to grow, the proportion and composition of green electricity in the production process of semiconductor companies have attracted more and more attention. For semiconductor companies, environmental awareness is not only a social responsibility but also a business return. Improving sustainability not only helps the long-term development of the company but also brings many practical benefits.
To achieve this goal, semiconductor companies can take a series of measures. First, strengthen technological research and development and innovation, and promote the research and application of green production technology. By developing more environmentally friendly and efficient production technologies, energy consumption and environmental pollution can be further reduced. Second, establish a sound green supply chain management system to ensure that every link in the supply chain meets the requirements of environmental protection and sustainable development. In addition, strengthening employee training and awareness enhancement, and cultivating a team with environmental awareness and sustainable development concepts, is also crucial.
By reducing energy consumption and waste emissions, companies can significantly reduce production costs. Secondly, as society's awareness of environmental protection increases, improving sustainability helps semiconductor companies attract and retain talent, and also wins more consumer trust and support. In addition, improving sustainability also helps reduce the vulnerability of the semiconductor supply chain, ensuring the stability and security of the supply chain.In the talent competition of the semiconductor industry, environmental protection also occupies an important position. The semiconductor industry is facing a competition for technical talent with several other industries, so maintaining a good environmental record is particularly important. Especially in attracting young employees, companies with a good record of sustainable development are more attractive. According to Deloitte's 2023 survey of Generation Z and Millennials, one-sixth of the respondents have already changed jobs or industries due to climate issues, and another quarter of the respondents plan to do so in the future. This trend indicates that the importance of environmental protection and sustainable development in the recruitment of talent in the semiconductor industry cannot be ignored.